Got Maltenes?
When it comes to asphalt pavement preservation, the magic is in the maltenes.
The goal of these pages is to explain the naturally resilient chemistry Pavement Technology refers to as Maltene Replacement Technology (MRT), and its demonstrative benefits in comparison with alternative methodologies for preserving asphalt pavements. Use the links below to delve more deeply into each concept discussed or use the form on this page to request a comprehensive white paper on this topic.
Check out the Spring 2020 issue of the Pavement Preservation Journal for the more information on MRT.
Sustainable Asphalt Pavements: The Science Behind Maltene Replacement Technology
In recent years, there has been no shortage of confusion (and some intentional misdirection) in the asphalt pavement preservation marketplace regarding the definition and understanding of maltenes and the role they play in rehabilitating and extending the life of asphalt roadways. Let’s clear up the confusion.
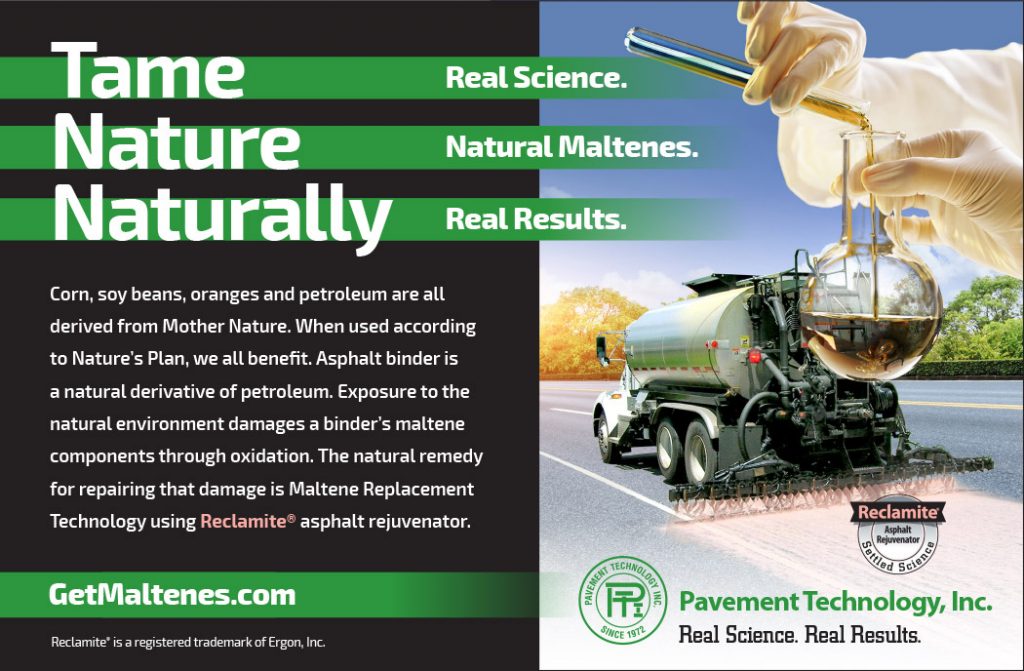
Independent Testing Confirms MRT Works As Promised
As defined by the U.S. government’s “Definition and World Resources of Natural Bitumens” 1 , maltenes are the n-alkane- (that is, pentane or heptane)-soluble molecular components of asphalt. There are two molecular structures common to all asphalts, regardless of their oil field source. Maltenes are basically the “glue” that binds asphalt pavements together, imparting flexibility, fluidity, and adhesion properties; asphaltenes are largely responsible for an asphalt pavement’s rigidity. Collectively, these properties are the key to an asphalt pavement’s ability to withstand considerable environmental and traffic stresses.
- As the more fluid resinous and oily fractions found in asphalt binder (aka asphalt cement), maltenes are characterized by a lower molecular weight than asphaltenes. They are also highly soluble, and chemically reactive (volatile).
- Asphaltenes are the more viscous substrate in asphalt. They are characterized by a heavier molecular weight, are not easily soluble, and are less chemically reactive.
- Polar Compounds 2(aka nitrogen bases)
- highly reactive petroleum resins that act as a colloidal dispersion stabilizer or “peptizer” for the asphaltene substrate, imparting distinct and necessary characteristics to asphalt pavements
- First Acidaffins (A1)
- aromatic resinous petro-hydrocarbons, with or without O, N and S, acting as a chemically compatible dispersion agent for the peptized asphaltene
- Second Acidaffins (A2)
- straight chain or cyclic unsaturated petro-hydrocarbons (olefins) that are somewhat oily and resinous, imparting distinct and necessary characteristics to asphalt pavements
- Paraffins3 (aka Saturates)
- straight or branch-chain saturated hydrocarbons (aka naphthene-aromatics) that highly oily and impart distinct and necessary characteristics to asphalt pavements
In 1959, Dr. Fritz Rostler, working in America’s petroleum and rubber industry with his associate Richard M. White, isolated and tested the chemical reactivity of asphalt’s two major components, asphaltenes and maltenes. They sought to identify what combination of these two molecular structures would most likely produce resilient thermoplastic performance.
By using sulfuric acid to separate the soluble components (highly volatile and reactive maltenes), and then using an n-pentane solvent to separate the insoluble components (heavier, more stable asphaltenes), they observed that the asphaltenes in asphalt, when exposed to lab-simulated sun and weather, increased over time. Meanwhile, the asphalt’s maltene content diminished. This suggested a continuously interactive molecular structure that would be receptive to maltene replacement treatments penetrating the asphalt matrix.
Once component separation was complete, Rostler et al. conducted abrasion-resistance (pre-weathering and post-weathering) and cohesion testing, which definitively demonstrated the loss of the low-molecular-weight maltene components in naturally stressed asphalt is largely responsible for the cracking and hardening seen in aging pavement. Subsequent analysis determined some maltene content is initially lost during the high-temperature asphalt production process, and more is depleted when the highly volatile maltenes in asphalt pavements are exposed to natural oxidation. The question then arose:
If the maltene content in asphalt pavements could be replaced, could the pavement’s flexibility and adhesion properties be restored?
Thus, genuine asphalt rejuvenation in the form of maltene-replacement technology was born, at least in theory. It was the Witco Corporation, the original manufacturer of today’s Reclamite asphalt rejuvenation technology, that undertook the research necessary to identify the most effective method for feeding maltene-rich chemistry to new and aging pavements.
Through their break-through examination of the chemical reactivity of an asphalt binder’s sub-components, Rostler et al developed ASTM Test D-2006-704 , which accurately identifies the relationships between the various maltene fractions with the goal of determining the optimal maltene content distribution within an asphalt rejuvenating agent. They did so by rank-ordering maltene fractions by their changeability or vulnerability to volatilization and oxidation. The observation was that the more vulnerable fractions are lost first and most often and thus should be the first and most often replaced by maltene-replacement technology.
This exercise, commonly known as the Rostler Analysis, is the measure still used today to determine the efficacy of a genuine asphalt rejuvenation treatment.
During the first half of the 20th Century, in the modern era of civil engineering, surface treatments such as coal tar were introduced in the hope of extending the life of existing asphalt pavements. It was soon discovered that coal tar is chemically incompatible with asphalt and therefore incapable of chemically bonding (fluxing) with an asphalt substrate. As a topcoat, coal tar can temporarily enhance the appearance of the underlying aging, gray asphalt pavement, but it wears off quickly and cannot be considered a rejuvenating agent.
Asphalt-based emulsions and fogs provide some temporal, surface-based protection of the underlying asphalt pavement from exposure to the elements. Although such emulsions share some chemical characteristics with authentic maltene-replacement asphalt rejuvenation, their maltene content has super-fluxed with the asphaltene content before being applied to the road. Asphalt emulsions and fogs are therefore incapable of molecular exchange with the original pavement and are useless as an asphalt binder rejuvenating agent. Only “free maltenes” can molecularly revitalize aged asphalts.
Maltenes, by definition, are petroleum-based. Chemistries derived from oranges, soy beans, corn or other so-called “natural” ingredients do not contain maltenes and are therefore incapable of replacing them. The Rostler Analysis of the chemical reactivity of a material’s asphaltene and maltene components cannot be used to measure the efficacy of bio-based chemistries because they have neither asphaltenes nor maltenes to fractionalize.
Some of the confusion in the marketplace over so-called “bio-based rejuvenators” may be attributed to the misplaced use of ASTM D2007SARA. SARA is highly useful as a generalized separation technique, applicable to a wide range of emulsion industries such as cosmetics, paints, wood treatments, and asphaltic fogs. It is not useful as a test for asphalt rejuvenation.
Most significantly, SARA may produce false positive results on bio-based products and other low-molecular-weight non-petroleum composites, including materials that are asphalt-damaging solvents. Powerful bio-solvents may appear to soften treated asphalts when, due to their high Kauri-butanol (Kb) value , they are actually chemically separating the asphalt matrix. If you wish to avoid using powerful solvents on your roadways, always inquire into the Kb value of the materials you are considering.
Historically, such materials were marketed as asphalt “releaser” agents because they promote dissolution of a petroleum suspension phase such as maltenes. In essence, elevated Kb value bio-based reagents destroy asphalt pavement through chemically-induced separation of the asphalt binder’s components. Once the asphalt matrix has been compromised, the damage may be irreversible and future maltene-replacing rejuvenation infeasible.
Although claiming to be eco-friendly, some bio-based reagents, despite their “natural” derivations, are substantially composed of ecologically damaging Volatile Organic Compounds (VOCs), which climate scientists believe to be ozone precursors toxic to humans.
The research is ongoing on bio-based materials. Raising specific questions about the chemical properties of any product you are considering is a good precaution to take before applying bio-based materials to your roadways.
In our work in the field, Pavement Technology is increasingly observing accelerated aging characteristics in newly built asphalt pavements. Societal pressures to use recycling asphalts and bio-based additives on America’s roadways may be contributing to this problem.
Recycled Asphalt Pavement (RAP) is recognized for its environmental and financial advantages. Typically RAP with higher quality aggregates is selected. If the use of RAP proves to be responsible for field problems, the mixing process and/or the additives used during reformulation are the likely culprits.
Specifically, in an effort to produce high temperature strength (reduced rutting risk) and low temperature fluidity (reduced cracking risk) during asphalt mixing, the mix additives and recycling agents used appear to be producing detrimental results in the field. If high Kb value solvents are used to affect high temperature / low temperature properties through asphalt binder viscosity reduction, the result may be the irreversible dissolving of the maltene phase.
Ultimately, the proof is in the pavement, and real-world testing5 further supports the results of Dr. Rostler’s analyses. For nearly 50 years, maltene-replacement technology has been used on asphalt roadways across America. During that time, a wide number of side-by-side (treated vs. untreated) pavement comparison studies have demonstrated the effectiveness of maltene replacement. Such true rejuvenators, which return molecularly exact, depleted chemicals into the asphalt matrix, extend roadway life when new pavements are treated within their first two years of service, then retreated three to five years later.
The initial treatment immediately restores those maltenes lost during the high temperatures used during asphalt mixing. The subsequent retreatments restore those maltenes depleted during exposure to sunlight and weather. Depending upon road conditions, additional retreatments are sometimes recommended, with the goal of achieving a multi-decade service life before pavement rebuild is required. Roadway longevity is the ultimate test of a sustainable solution, and Maltene Replacement Technology (MRT) is both lab-tested and field-proven to extend the life of asphalt pavements.
- https://pubs.usgs.gov/b
- Vladimir Kalichevsky and Stewart C. Fulton, 1931 patent US1926523A
- Heavy Oil Science Center, More About the Chemistry of Asphaltenes and Maltenes, Foster Learning Inc. (http://www.lloydminsterheavyoil.com/asphaltenes2.htm)
- https://www.pavementpreservation.org/wp-content/uploads/2017/03/FPPC335_Asphalt_Rejuvenation.pdf
- https://www.pavetechinc.com/wp-content/uploads/2019/02/Charleston-County-Viscosity-Charts-022619.pdf